Near-Infrared Furnaces
Advanced production and laboratory infrared controlled atmosphere belt furnaces manufactured to your application requirements. Infrared furnaces and dryers offer unique infrared lamp and heating chamber technology to provide outstanding performance and low cost of ownership. Select by furnace application or model.
HEATING TECHNOLOGY. All furnaces heat product by means of radiation, convection and conduction. LCI furnaces and dryers use quartz near-wave IR lamps as the primary heat source to emphasize the radiation component. Process gas, introduced into heating chambers through the porous ceramic insulation in a controlled flow, provides some convection heating, while the continuous belt running through the furnace provides some conduction heating to parts being carried, as well.
PERFORMANCE. Outstanding performance is achieved with extremely precise temperature and atmosphere control. Temperatures can be maintained to +/-2°C across the belt away from the edges. Within the heating section, the process gas is uniform, ultra-clean and never recirculated. Pressurized process gas is forced through the porous ceramic insulation as it enters the heating chamber creating a pre-heated, laminar flow process gas. In this uniform, stable atmosphere, the process window becomes broad and repeatable. Process atmosphere is controlled much like a clean room. Controlled eductor exhausts at either end of the heating section and in the optional burnout zone(s) maintain process gas balance to keep outside air from entering the furnace.
PROCESS GASES. These advanced design furnaces and dryers run thermal processes in CDA (clean, dry air), nitrogen, forming gas with premixed hydrogen and nitrogen, and forming gas with in-furnace mixed hydrogen and nitrogen atmospheres. Automatic control of process gas selection is available.
SELF-CORRECTING. Small zones and high temperature differentials enable broad profile flexibility. Temperature is maintained with control thermocouples above the belt in each zone to quickly sense incoming cold mass. Quartz IR lamps inside the chamber instantaneously adjust their output to achieve tight temperature control. Profiles are repeatable regardless of the loading. Each load sees the same temperature. No “dummy load” is required. Profiles with peak temperatures from 100°C to 1000°C are possible.
COOLING. The closed atmosphere cooling tunnels provide convective cooling with a controlled flow of process gas. This gas protects the product while cooling it to a safe temperature. Heat is removed from the tunnel walls by external fans or by optional water cooling. Fan-driven ambient air cooling is also an option when your thermal process allows its use.
INSTANT ON. Unlike conventional furnaces, this furnace can be turned on, turned off, or re-profiled in minutes, saving time and money. Low cost of ownership results from the furnace versatility, compact size, high throughput, quick readiness, and low utility consumption.
Efficient Lamp IR Heat
POWER TO THE HEATING ELEMENTS (LAMPS). Our standard IR furnaces and dryers use tungsten filament halogen lamps. The lamp envelope is quartz glass, the tungsten filament supplies a high luminous output per watt, and the “halogen cycle” minimizes evaporation of the tungsten filament. Light intensity and color temperature remain stable throughout the life of the lamp. Lamp service life in typical applications is about 6000 hours at full power and typical power operating conditions for a furnace zone are usually less than 20%.
HIGH TEMPERATURE MODELS (SiC models). Select furnace sections or entire heating chamber can be fitted with silicon carbide (SiC) elements which allow operation up to 1150C. These elements are not as fast as the standard quartz tungston. However, they still provide tight control in a wider temperature range.
PHASE-FIRED SCRs smoothly control power to the lamps based on control signals from a PLC digital output module controlled by an industrial rack-mounted computer. “Soft Start” technology is built into the controls to minimize the initial in-rush of power on furnace warm up. IR lamp controls automatically compensate for changes in the facility power line voltage to keep the selected IR radiation spectrum constant.
Hot on Demand
Radiant heat is highly focused and selective as experienced by one standing alternatively in the sun and shade on a cool day. Radiant infrared heat directs energy to production parts, not the surrounding atmosphere. When an IR furnace is started, lamps reach full temperature almost immediately. Zones will ramp from ambient to 1000°C in minutes and usually stabilize at process ready within 20 minutes. Radiant furnaces allow larger differences between zone temperatures to be programmed and successfully achieved than with convection furnaces.
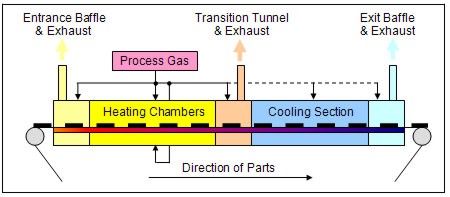
Typical Near-infrared Belt Furnace Sections
Process Gas Introduction and Self Cleaning
These near infrared furnaces are designed so that process gas (CDA, Nitrogen or Forming Gas) is introduced into the furnace chambers through porous ceramic walls. When properly adjusted, the continuous flow of process gas keeps drives the infrared elements ON and inhibits collection of particulate and other deposits on the furnace walls. The process gas is pulled from the heating zone toward the entrance via eductors evacuating VOC's and other undesirable elements from the furnace chamber.
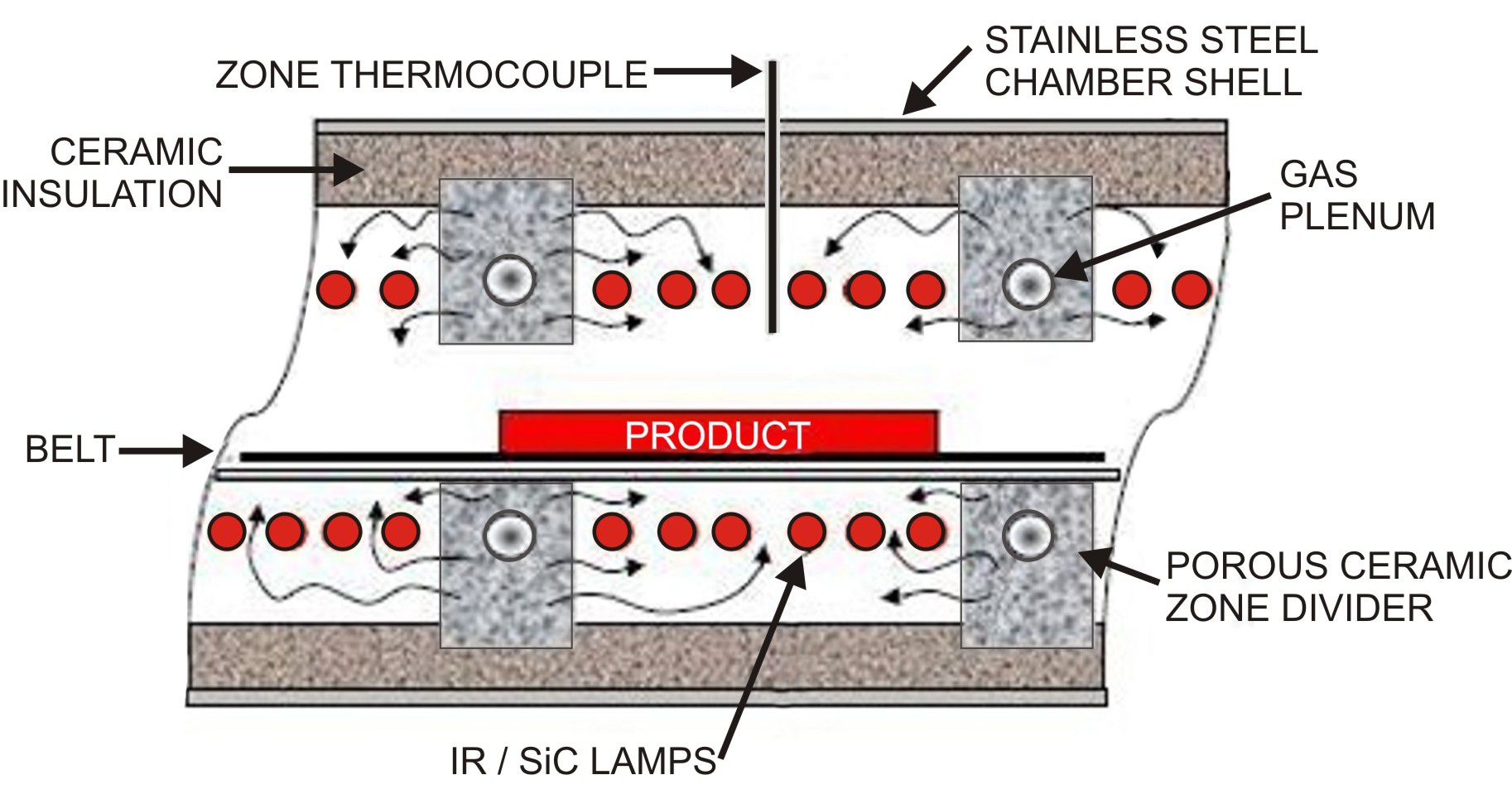
Introduction of Process in the IR Furnace Chamber
The preferred method of introduction of process gas in an IR furnace is through the furnace walls with gas supplied in the first zone at twice the rate as in subsequent zones. Process gas and volatiles are drawn toward the entrance of the furnace and out a venturi assist exhaust stack.
Multiple Controlled Atmospheres
For most processes the clean dry air (CDA) is an effective and economical process gas. Alternately furnaces can be configured for Nitrogen (N2) throughout, or with multiple gases: nitrogen at the entrance and exit to drive out oxygen and forming gas (FG) or even Hydrogen introduced into the heating chambers. If lower process gas consumption is desired, CDA can be used for the exhaust eductors and even the cooling gas where product temperatures are below the oxidizing temperature.
H2/N2 MIXING. With Hydrogen/Nitrogen mixing, process engineers can vary the H2/N2 mixture to the heating zones by zone to suit varying requirements. With H2/N2 mixing the system can be adjusted to allow almost pure hydrogen in critical high temperature zones of the furnace. Individual zone adjustments for both Nitrogen and Hydrogen allow for fine tuning the mixture by zone to improve performance tune for lower cost.
When hydrogen is not required, a software switch converts the furnace to a nitrogen only furnace thereby bypassing the additional safety checks required for H2 enabled operation and saving production time.
Hermetically sealed furnaces include plenem boxes covering the element chamber penetrations.
IR Heating Elements
HEATING BY INFRARED RADIATION is a direct form of heating where the infrared emittor or lamp radiates energy that is absorbed directly by the product. Because IR heat energy is conveyed directly to the product where it is converted into heat rather than through an intermediate medium like air, IR furnaces are inherently high-energy efficient systems.
Our furnaces are manufactured with specially designed high quality quartz infrared heating elements that are controlled to emit clean near-infrared energy. Shortwave energy of near-infrared (NIR) emitters penetrates deeper than longer wavelengths of medium and far infrared sources. Benefits of near-infrared systems are numerous:
Advantages of Near-Infrared Technology | |
---|---|
Immediate responding heat source (<1 second) | Efficient use of applied energy |
0-100% control of heat output | Eliminates need for extended preheating |
High thermal differential between source and product promotes rapid efficient direct thermal transfer | Minimal amount of supply process gas required |
Process flexibility and energy savings | Minimal amount of exahust gas emitted |
Ramp and hold capablility | Consistent product quality |
Compact design uses minimal space | Clean energy source |
Enhanced End Product Performace | Shorter process times |
FAILURES UNCOMMMON. Our OEM elements incorporate a design feature that reduces temperature at the ends, a common failure point in heating elements. These special elements are proven in the field and continue to be manufactured in Germany, Japan or USA as they have been for over 30 years.
OTHER HEATING SYSTEMS. In contrast, many low cost furnaces are often made with ceramic fiber insulated heaters that use helically wound resistance wire elements embedded in preformed rigid panels of vacuum-formed refractory fiber. These systems depend upon low weight thermal mass and thermal conductivity in order to handle rapid cycling. Small diameter element coils are kept to a minimum reducing the difference between the element and chamber temperature to diminish the risk of element failure.
SACRIFICES WITH CONVECTION TECHNOLOGY. In many applications convection-only technology sacrifices the benefits inherent in thermal processing using a near-infrared energy source. The difference is especially evident in thick film, solar cell, and many curing and drying appplications where near-infrared radiation not only is the lowest total cost solution, but produces an end products which exhibit a special performance boost.
Heating Element Replacement
For low (80-400°C to medium (400-650°C) temperature applications, IR heating elements almost never need replacement. In fact many low temperature systems have been in service for well over 7 years without a single lamp replacement. At higher temperature, element life is shortened as a function of the operating temperature. If an element does fail, the furnace immediately compensates for the element that is out of service until it can be replaced.
Lamp replacement is easy and special skills are not required. With the furnace at ambient and power disconnected, it usually takes as little as 15-30 minutes to replace a failed element on non-hermetic furnace. For furnaces with hermetic sealing (HC), replacement can be completed in 30-45 minutes. (see TEC-250) Generally recalibration of the furnace is not necessary because an IR lamp is replaced.
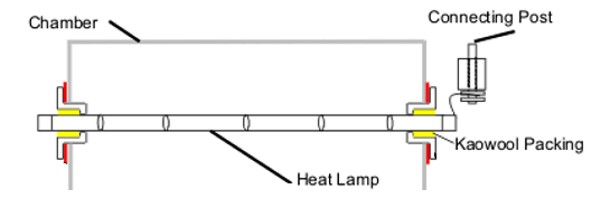
Cross-section of Furnace Chamber Showing Near-IR Heating Element